

Reasonable efforts to reduce pressure losses yet increase flow rates are of significant value for both the scientific and the engineering fields. There is a design balance between minimization of pressure loss and maximization of flow that is often sought by a fluid engineer. It should be noted that “minor” losses are often significant components of pressure loss within a system. Minor losses, on the other hand, are associated with pressure drop that occurs when the flow passes through some obstacles in the piping system, such as a bend, a valve, an orifice plate, a change in diameter, or other. Friction pressure losses refer to pressure drop caused by friction between the fluid and the bounding wall. Pressure variations within piping systems are a result of so–called “friction pressure losses” and “minor pressure losses”. Great efforts have been made to optimize fluid systems and these optimization efforts generally involve the maximization of fluid flow and/or the minimization of pressure loss. In particular, the relationship between flow rate and pressure variation is critical and is among the most studied problems in fluid mechanics. Keywords: dimple geometry, pipe, recirculation, flow resistance, pressure drop, flow rate, wall mass IntroductionĪn understanding of fluid flow through pipes and ducts is a fundamental requisite for the design and optimization of fluid–flow systems. These findings allow optimization of hydrodynamic performance when a balance between pressure drop, flow rate, and wall mass transfer is required. Once the dimples become sufficiently large to allow recirculation, there is an inverse relationship between flow rate and pressure drop. For dimples whose sizes are small enough to prevent recirculation, the flow resistance is constant with dimple size. The flow patterns within the dimple are connected to changes of hydrodynamic resistance. On the contrary, as the dimple diameter increases, a recirculation zone forms and moves in the downstream direction for increasing dimple size. It was found that for small dimples, the flow does not enter into the dimple to forming a coherent recirculation zone. Using a periodic solution domain, in–line dimples were simulated with diameters that varied from 0.125mm to 2mm (with a pipe diameter of 6 mm). We'll verify the results by following a systematic process which includes comparing the results with the analytical solution in the full-developed region.Laminar flow through a dimpled pipe has been investigated with a focus to determine the relationship between hydrodynamic resistance and dimple geometry.
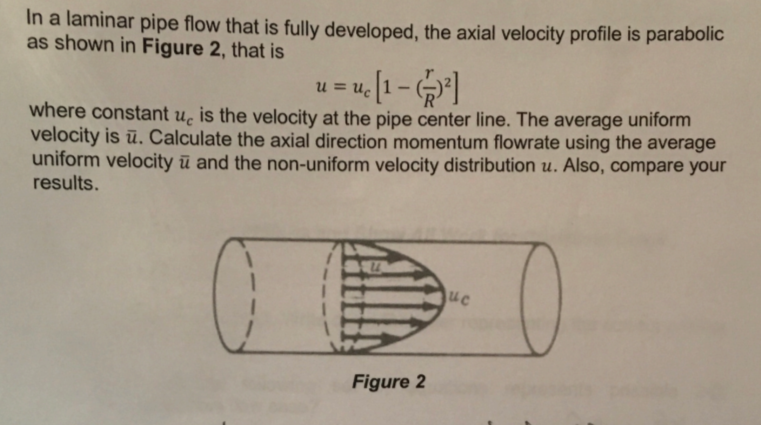
We'll solve this problem numerically using ANSYS Fluent. Take density ρ = 1 kg/ m 3 and coefficient of viscosity µ = 2 x 10 -3 kg/(m*s). These parameters have been chosen to get a desired Reynolds number of 100 and don't correspond to any real fluid. The pressure at the pipe outlet is 1 atm. The pipe diameter D = 0.2 m and length L = 3 m Consider the inlet velocity to be constant over the cross-section and equal to 1 m/s. This module is drawn from MAE 4230/5230 Intermediate Fluid Dynamics at Cornell University.Ĭonsider fluid flowing through a circular pipe of constant radius as illustrated below. Connect the ANSYS steps to concepts covered in the Computational Fluid Dynamics section.
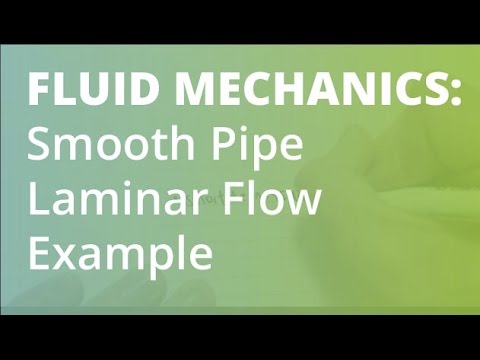

The edX interface provides a better user experience, so we have moved the module there.
LAMINAR FLOW PIPE FREE
This module is from our free online simulations course at edX.org (sign up here).
